Stover Makeover
Last fall, as soon as combines left the corn fields surrounding York, Nebraska, a veritable army of tractors pulling flail shredders and large square balers moved in for a highly coordinated second harvest. The race was on to get excess crop residue—corn stover—shredded, put in windrows, baled and stacked for transport...
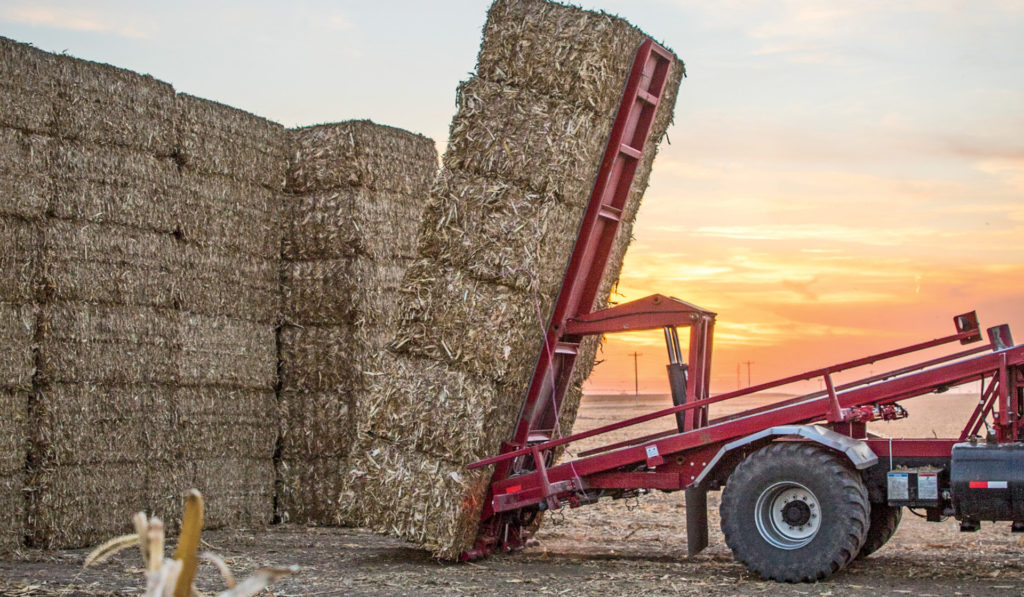
Stover Makeover
Last fall, as soon as combines left the corn fields surrounding York, Nebraska, a veritable army of tractors pulling flail shredders and large square balers moved in for a highly coordinated second harvest. The race was on to get excess crop residue—corn stover—shredded, put in windrows, baled and stacked for transport...Last fall, as soon as combines left the corn fields surrounding York, Nebraska, a veritable army of tractors pulling flail shredders and large square balers moved in for a highly coordinated second harvest. The race was on to get excess crop residue—corn stover—shredded, put in windrows, baled and stacked for transport to a unique new processing plant, all in time to beat the region’s typical late-autumn rains and get farmers back in the field for tillage.
The destination of these 145,000 bales of stover was the new, first-of-its-kind $30 million Pellet Technology USA plant in York. There, the stover is tracked, cleaned, tested and processed into three lines of unique pelleted cattle feeds. The company also has a larger vision of its role—converting an underutilized resource into a benefit for growers and livestock producers, as well as for the environment.
“We want to make sure that everything is a win for the farmer,” says Joe Luna, manager of business strategy for PTUSA. “They have less residue to hassle with; they have an additional income stream; they have less management and labor. Then we have a product that is uniform and provides a sustainable, traceable and performance value for livestock feeders.”
Instead of building a cellulosic ethanol biorefinery to use the stover, PTUSA shortens the path by putting it into nature’s cellulosic biorefineries—cattle. And because pellets are as easy to transport as grain, Luna says, “If there is a drought in California, we pick up the forage from here and send it to farmers there on a train.”
Using corn stover for cattle feed is not new. Until now, however, it meant turning out cattle to forage on corn stubble or harvesting the stover to be chopped, ground and mixed with an alkali treatment such as quick lime to improve digestibility, not knowing precisely what nutrients were delivered to the animal.
“By us being able to utilize corn stover as a base for our pellets,” Luna continues, “we’re able to provide more consistent nutrients, more consistent performance and a better value option for feeders.”
Its tight quality controls and a short harvest window led PTUSA to seek out third parties with the expertise to manage the process of getting the stover from fields to the pellet plant. One such partner is AGCO, which, through its Strategic Segment Solutions group, oversees and implements the feedstock harvest program.
In addition to providing equipment, such as tractors, shredders, balers and stackers, AGCO manages the logistics of the dozen or so harvesting teams. Through one of its dealerships, Butler Ag Equipment, the company also provides service to those machines, while Osceola Implement, the local AGCO dealer for farmer retail needs in York and the eight surrounding counties, continues to offer customers excellent service and sales.
“What AGCO does,” says Glenn Farris, director of AGCO Strategic Segment Solutions, “is provide a lot of the glue that holds all of the things together. We’ve learned to bring a type of industrial efficiency to on-site service and attention.” At the same time, the AGCO team members use their agronomic expertise to be sure the needs of the farmers are met as well.”
See the full story and a video of the harvesting operation in action at https://www.myfarmlife.com/features/stover-makeover/.
Written By: Marilyn Cummins