AGCO’s Jackson Plant: Better, Stronger, Faster
Imagine taking a brand-new tractor, worth tens of thousands of dollars, and purposefully trying to break it. That’s what the folks at the AGCO manufacturing facility in Jackson, Minn., do just about every workday. It all happens at Jackson’s Quality...
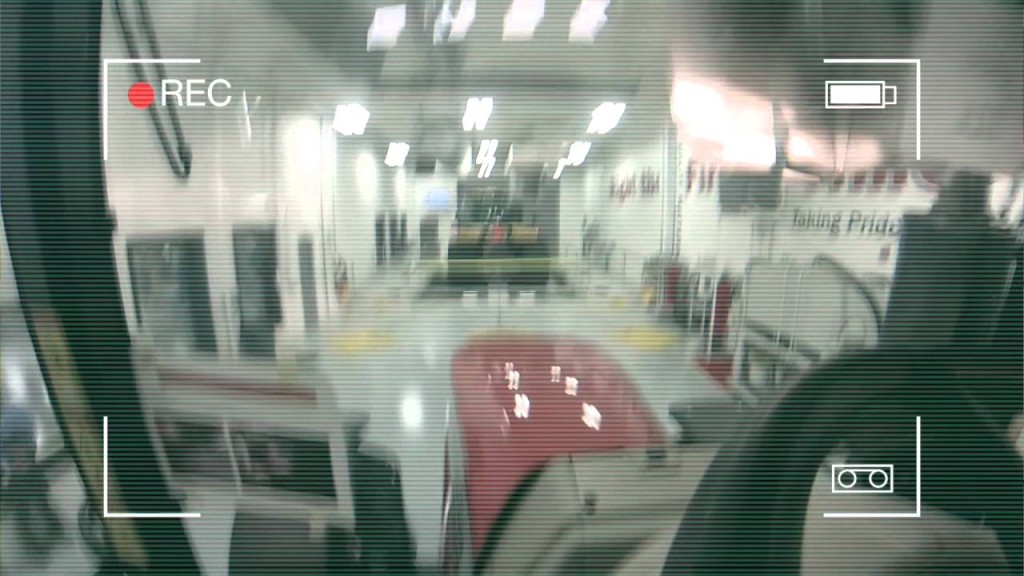
AGCO’s Jackson Plant: Better, Stronger, Faster
Imagine taking a brand-new tractor, worth tens of thousands of dollars, and purposefully trying to break it. That’s what the folks at the AGCO manufacturing facility in Jackson, Minn., do just about every workday. It all happens at Jackson’s Quality...Imagine taking a brand-new tractor, worth tens of thousands of dollars, and purposefully trying to break it. That’s what the folks at the AGCO manufacturing facility in Jackson, Minn., do just about every workday.
It all happens at Jackson’s Quality Gate Five. The $1.97 million-facility can hold and check two tractors at once, one on the “jounce” and PTO testing station, and the other on a chassis dynamometer.
For the jounce test, a tractor’s rear wheels or tracks are positioned on pads that rock back and forth. This test is used to verify that there are no loose fittings, hoses or electrical connections. Afterward, the tractor is physically inspected to make sure nothing came loose as a result of the shaking, which is so violent no one is allowed to be in the cab.
While still at the first station, the PTO is tested at various speed and load levels, and its output measured across the rpm range. Each tractor is then moved to the second station and the chassis dynamometer. Here, a multi-roller bed is used to verify different functions like the steering, brake, transmission shift quality, DEF functionality and limited powertrain performance.
Six winches hold the tractors in place as they speed up to 33 mph and rev to as high as 400 HP. The dynamometer reads the engine rpm, what gear it’s in and how well it shifts, and when it shifts, how low the rpm goes.
“What we learn,” says Eric Fisher, the plant’s director of operations, “also affects what we do upstream.”
Overall, according to Fisher, the work in Gate Five takes about two hours, and includes 250-plus tests and the analysis of more than 150,000 data points. In just the first month of operation, the inspections, he says, “yielded a 25% reduction in defects, and that’s just a start.”
“Like its customers, AGCO doesn’t embrace technology for its own sake,” says Bob Crain, AGCO Senior Vice President and General Manager, Americas. “There must be a return on investment.”
The expansion and upgrades at the Jackson plant, as well as those throughout the company’s global facilities, offer just that, says Crain, “in the company’s relentless pursuit of its stated goal—to be No. 1 in customer-perceived quality.”